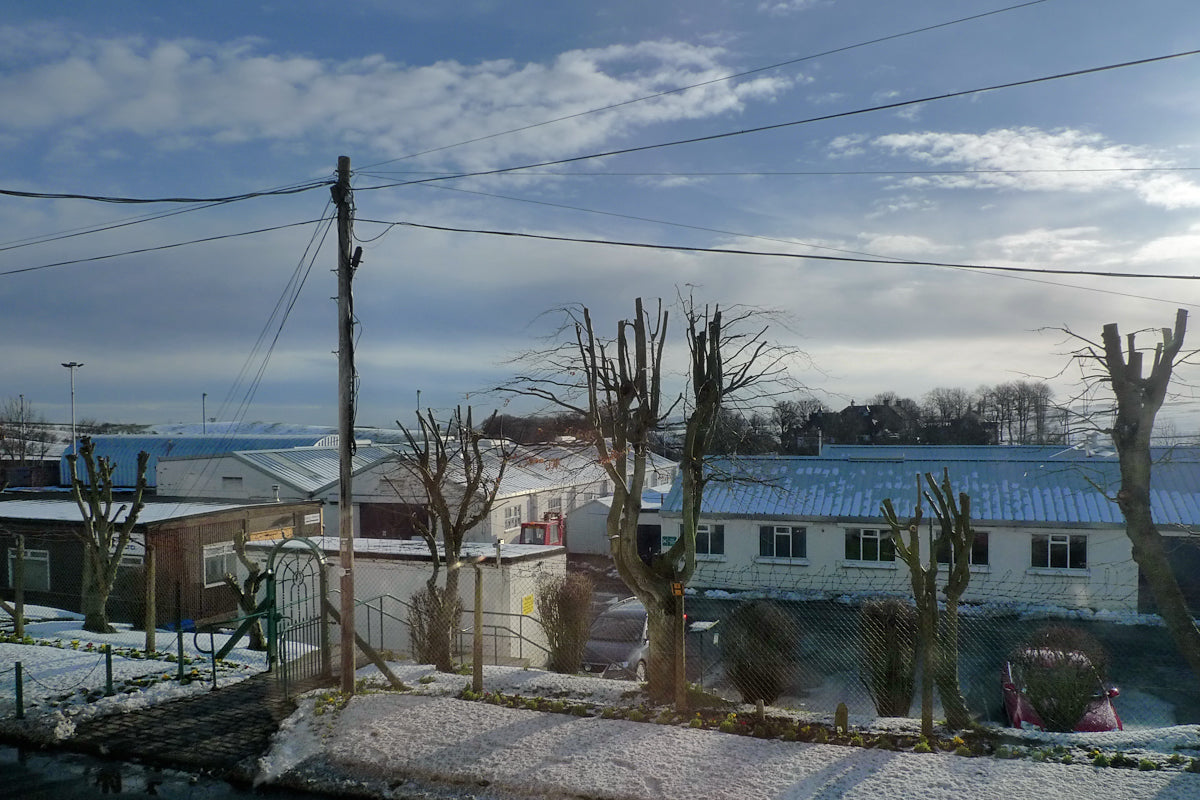
Where we are based
Headquartered in Loanhead near Edinburgh, MacScott Bond operates as a strategic hub for stocking and distributing pneumatic, motion control, and hydraulic components.
Certified to ISO9001, the Loanhead Division exemplifies the company's dedication to quality and reliability. As stockists and distributors for reputable brands such as Globe, Atlas Copco, MP Filtri, and ACE controls, MacScott Bond ensures that its customers have quick access to a comprehensive range of components.
The division can also offer tailored solutions for pneumatic, oil, or water hydraulic and cooling systems, catering to diverse industrial needs. Whether clients require components for new projects or replacements, MacScott Bond's Loanhead Division remains steadfast in its commitment to providing quality products and services.
Our hydraulic repair service typically includes several essential components to ensure the effective restoration of hydraulic equipment. Here's a general overview of what you can expect from a hydraulic repair service:
- Inspection and Assessment:
The first step is a thorough inspection of the hydraulic equipment. This involves identifying the issues, damage, or wear and tear that may be affecting its performance.
- Disassembly:
In many cases, the equipment may need to be disassembled to access and diagnose internal components accurately.
- Cleaning and Fluid Replacement:
The hydraulic system may be cleaned, and hydraulic fluid or oil may be drained and replaced with fresh fluid to ensure optimal performance. Filters may be cleaned or replaced as part of the service.
- Component Repair or Replacement:
Damaged or worn components, such as hoses, seals, valves, pumps, and cylinders, will be noted, with a full report and quote made up for your evaluation. If agreed, we would then replace this equipment.
- Testing and Calibration:
After repairs or replacements, the hydraulic system is tested to ensure it operates correctly. This may involve pressure tests, flow tests, cleanliness tests and other performance evaluations.
- Safety Checks:
Safety features, such as pressure relief valves and emergency shutdown systems, are tested to ensure they function correctly.
- Documentation:
A comprehensive report detailing the repairs, replacements, and testing results is typically provided to the client for record-keeping and future reference.
- Recommendations:
MacScott Bond may offer recommendations for ongoing maintenance practices or upgrades to improve the hydraulic system's performance and longevity.
It's important to note that the specific services included in a hydraulic repair can vary depending on the equipment's type, complexity, and our experience with the systems. Therefore, it's advisable to discuss the details of the service with MacScott Bond to ensure your specific needs and requirements are met.
Air Motors are a little easier to predict for us. We offer a service for all Globe air motors. A service for air motors typically involves the same series of steps to ensure the efficient operation and longevity of the air motor. Here's a general overview of what you can expect from a service for air motors:
- Disassembly:
The air motor will be disassembled to access internal components for inspection and maintenance.
- Visual Inspection:
The service begins with a visual inspection of the air motor. This involves checking for any visible damage, wear, or signs of contamination.
- Cleaning:
The air motor components are thoroughly cleaned to remove dirt, debris, and contaminants that may affect performance or cause further wear when back in operation.
- Component Inspection:
Internal components, such as vanes/pistons, bearings, seals, and gaskets, are inspected for wear and damage. Any worn or damaged parts are identified for repair or replacement. Typically, we will replace seals and gaskets. A full report and quote is generated for your evaluation. If agreed, we would then replace the necessary equipment.
- Reassembly:
After necessary repairs or component replacements, the air motor is reassembled with care to ensure all parts are properly aligned and secured.
- Testing:
The air motor undergoes testing to verify its performance.
- Documentation:
A detailed report is typically provided, outlining the work performed, any repairs or replacements made, and the results of performance testing.
- Recommendations:
We may offer recommendations for ongoing maintenance practices or upgrades to the airline required to enhance the air motor's performance and reliability.
We stock genuine spare parts for the air motors that we sell at MacScott Bond. If you have another model of air motor that you would like us to take a look at, we may request the manufacturer’s O & M Manual. When arranging a service for your air motor, it's advisable to discuss your specific needs and requirements with MacScott Bond to ensure we can meet your expectations.
As an authorised Accumulator Recertification Centre with personnel specially trained by leading manufacturers, our Aberdeen division can offer a full repair and certification service in accordance preferred British Standards. In addition, MacScott Bond Aberdeen undertake painting to commercial and offshore specifications, nitrogen pre-charge and flushing to industry standards as well as arranging third party inspections for the customers.
Any questions?
If you have any queries, need a quote for one of our products or want some technical advice from one of our engineers, please get in touch and a member of MacScott Bond will assist.
Our workshop and their vast experience in building fluid power systems of all shapes and sizes are able to investigate and repair a wide array of equipment.
To find out if we can help, get in touch with us on the number below and arrange for your hydraulic or pneumatic equipment to be delivered to our stores for inspection.
0131 448 2950
enquiries@macscott.com
